Pier Foundry (U.S.A.)
“By using Sinto’s automated-pouring line, Pier is able to run over 300,000 molds without the need for any major repairs.”
Pier is an ISO 9001-certified producer of gray and ductile iron calcium.
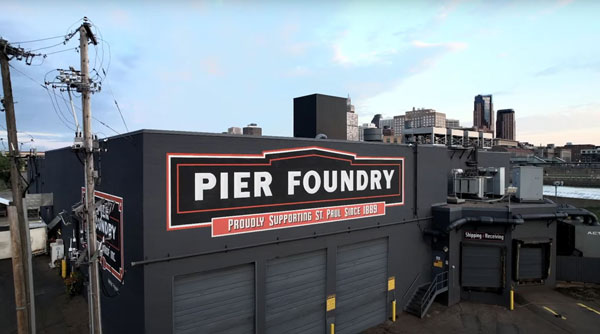
Pier Foundry has evolved from a small but great foundry in 1889 to a highly-automated molding electric melting and material handling operation. They’re one of the longest-existing foundries in the Twin Cities, sitting right on the banks of the Mississippi River, across from downtown St. Paul, Minnesota. They’re an ISO 9001-certified producer of gray and ductile iron calcium. Their top industries are heavy duty truck agriculture pump and valves, and construction.
Sinto’s 20x24 mold machine is a game changer for Pier, allowing it to go from 10 molds per hour to 100 molds per hour or more.
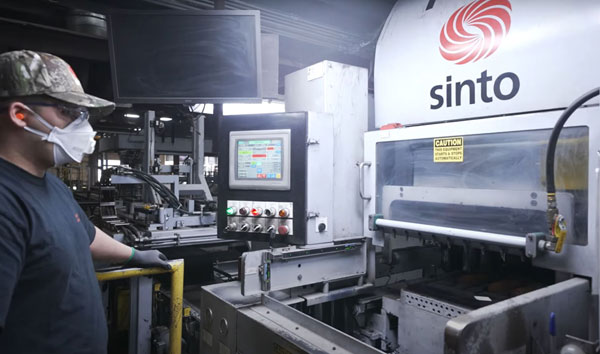
Pier has been working with Sinto since 2010 on improving quality speed and production. In 2020, Pier replaced their manual cope and drag line and installed Sinto’s 20x24 mold machine, the FB0-III.
It’s been a game changer for them, allowing them to go from 10 molds per hour to 100 molds per hour or more.
In addition to increased production, Pier saw an increase in consistency and quality, as well as a decrease in lead times with the FB0-III.
This helped increase capacity and optimize lead times across all other lines and iron types.
Feedback provided by Sinto’s Industry 4.0 analytics allows Pier to manage maintenance and other issues to prevent downtime.
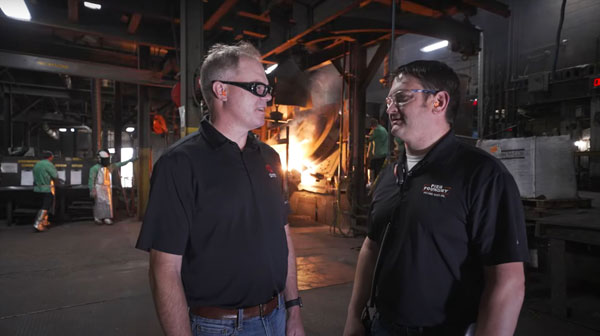
FBO-III has sensing equipment all over it. It means that Pier is able to track the individual movements of basically every piece of the machine, identify when potential issues are arising, and correct them before they become issues in their line. Sinto also helps them monitor air quality and improve employee safety.
In addition, Sinto helps with dust-collection monitoring and remote monitoring of some of their bearings and gearboxes throughout the facility.
With this new system, the pouring line is all automated, and weight and jacket transfers are also all automated. This has reduced back strain injuries on that pouring area, which has been obviously very important in employee safety.
“This is one of the best things that we have going with Sinto, to able to run over 300,000 molds without a major repair,” they expressed. Pier doesn’t see a major repair in their future so long as they do part in taking care of their equipment.
Pier are looking towards the future in which they can continue to partner with Sinto.
Sinto has a lot of resources that Pier Foundry leans on. Sinto has been a great partner for Pier Foundry, providing many other foundry services. Pier are communicating with Sinto and really looking towards the future of how they can continue to partner with each other.
Company Profile
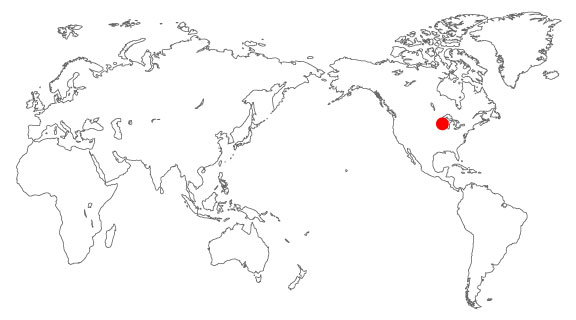
- Name:
- Pier Foundry
- Location:
- U.S.A.
- Products:
- Gray and Ductile iron castings
- Sinto products:
- FBO, remote monitoring